

Control of the valve by regulating pressure.Ģ3 Unloading valve Regulating pressure Air inlet Spring loaded Vent HoleĢ4 Unloading valve LOAD UNLOAD Regulating pressure Air inletĢ5 Check valve Check valve is integrated in the unloader for Series 6 compressors (XAS 185, 375, 400) Closes when the compressor is stopped. Open position at load condition => Air consumption Closed position at no load condition => No air consumption. Only one rotor is driven, this rotor then drives the other one : old XAS 90 : female driven rotor all other compressors : male driven rotor When required a gear box or drive belt brings the compressor element to the correct speedįour major running conditions : NO-LOAD Machine started, minimal pressure build-up LOAD Receiver tank pressurized and air consumption UNLOAD Receiver tank pressurized, no air consumption BLOW-DOWN Machine stopped, blow-off of air pressureġ9 Air system Air filter Compressor Element (AFCE) (with vacuator valve VV, Safety Cartridge SC and vacuum indicator VI) Unloading Valve (UV) Compressor Element (CE) Temperature Switch (TS) Check Valve (CV) Air Receiver (AR) Non Return Valve Minimum Pressure Valve (MPV) Air Outlet Valve (AOV)Ģ0 Air filter Filtration of the inlet air in 3 stages :Ĭentrifugal dust separation paper filter element safety cartridge (optional) Vacuum indicator gives an indication when the pressure drop over the filter element is too high filter element needs to be replacedĢ1 Air filter Centrifugal separation Air inlet Vacuum indicatorįilter element Dust to compressor elementĢ2 Unloading valve Opens and closes the air inlet to the compressor element.

Oil is injected in the bottom of the rotor housing, onto the bearings and gears, and discharged with the compressed air Oil is used for : Cooling : compression heat is absorbed by the oil Lubrication of rotors, bearings, gears Sealing between rotors and rotor and housing Corrosion protection of the internal metal parts Lower efficiency because of internal leaks High quality bearings on the rotors required rotor clearances are small axial bearings needed Noise level (high frequency) High quality finishing of the rotors required expansion of rotors through heat results in blocked elements
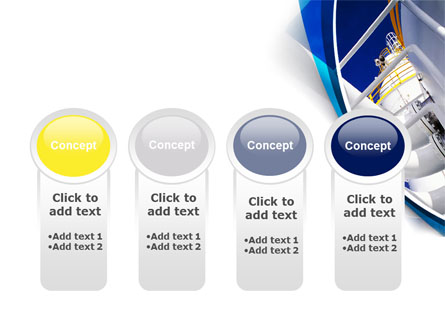
Low wear : guaranteed long life time and constant capacity life time is determined by the bearing wear Absolute oil free design possible No inertia forces vibration free operation high speeds possible big power possible High shaft speeds and large flow rate : gives small exterior dimensions Simple and strong design : no valves and seals reliable and maintenance friendly small dirt particles improve the sealing and the efficiency almost pulsation free air Suction Compression start Delivery Compressionġ0 Pressure Ratio Each screw element has a fixed, integrated pressure ratio This depends on : length of the rotors Pitch of the screw form of the discharge port Best efficiency is reached when the pressure ratio is adapted to the required working pressure Symmetrical screw was changed to an asymmetrical helical profile 10% more efficiency
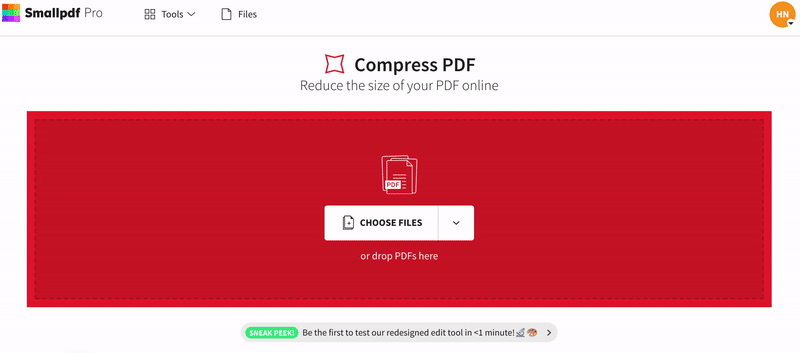
Male and female rotors move towards each other, while the volume between them and the housing decreases.Ĩ Screw Compressor Screw profile improved in 1966 Atmospheric pressure absolute effective total pressure pressure = 0ģ Effective pressure The effective pressure is the difference between absolute pressure and atmospheric pressure It is the pressure available to deliver work Absolute pressure 8 bar (118 psi) Atmospheric pressure 1 bar (15 psi) Effective pressure 7 bar (103 psi)Ĥ Effective pressure XRVS 455 Md : receiver pressure during unload is 27 bar (397 psi) Forces on the air receiver cover (0.08 m²) is more then 22,000 kgf (about 48k pounds)ĥ Free Air Delivery Free Air Delivery : is the measured “real” delivered volume of air (in l/s or m³/min or cfm) at the same conditions of pressure and temperature at the air inletĦ Free Air Delivery FAD is not equal to the displacement volume of the compressor element, because internal losses in the element (leaks to air inlet) FAD is independent from the ambient conditions (temperature & pressure)ħ Screw Compressor Introduced in 1958 by Atlas Copco
